【Abstract】Wood is an indispensable main material for economic development. It not only occupies a very important position in industrial and agricultural production, but also is an indispensable material in the process of people’s life. At present, with the continuous development of the wood processing industry and the continuous improvement of the technical level, the use of wood has become more extensive. Wood is a natural organic material. It has special properties of its own, and these properties are very closely related to the structure of the wood itself and the growing conditions. Therefore, compared with other materials, wood has its own advantages and disadvantages. When choosing wood, it is necessary to use new technologies and new methods to improve its own advantages and disadvantages, improve its performance, and meet the goals of rational use and wood saving. Therefore, in order to ensure the processing and utilization rate of the wood itself to a great extent and reduce the quality problems of the final product, it is necessary to select dry wood as much as possible. This paper analyzes and summarizes the effective application of wood drying theory in the technical process of wood processing.

Wood drying theory:
Wood contains varying amounts of moisture. Moisture in wood also varies with tree species, tree age, and the season of felling. In order to ensure the quality and service life of wood and wood products, practical measures must be selected to minimize the moisture in the wood as much as possible. If you want to reduce the moisture content of the wood itself, then you must increase the temperature of the wood itself, so that the moisture contained in the wood can evaporate from the inside to the outside, and in the air with a certain flow speed, the moisture can quickly escape from the wood, thereby achieve drying goals. In order to ensure the quality of wood, it is necessary to control the humidity of the drying medium, so that it can achieve a fast and high-quality drying effect of wood. Such a process is also called wood drying. Because the above method is to choose the form of convection heat transfer, a way of heating and drying from the outside of the wood itself, therefore, it is also called convection drying. In general, the theory of wood drying is a process in which water is discharged from the wood in the form of evaporation and vaporization.
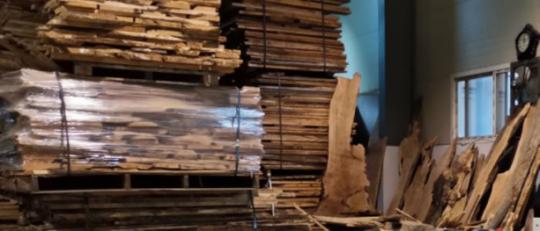
The significance, principles and optimal drying methods of wood drying in wood drying:
1.1 The significance of wood drying application in wood drying:
The wood itself has relatively low density and relatively high strength. In addition, it also has acid and alkali corrosion resistance and strong insulation properties, which can quickly complete cutting, beautiful texture and color and other very good properties. Very large amounts of wood are used in several parts of the economic development of some countries, such as construction, machinery and vehicles, ships and textiles, as well as agricultural implements, as well as furniture, musical instruments, and aviation. However, if the product is made of wood that has not been dried, the quality of use cannot be guaranteed, so the wood must be properly dried.

1.2 Basic principles of wood drying:
The basic principle of wood drying itself is to continuously improve the drying speed on the basis of guaranteeing the drying quality, and save the energy loss as much as possible, thereby reducing the drying cost. Drying quality currently mainly refers to: the moisture content and drying uniformity in the dried wood must be consistent with the specific processing requirements; at the same time, the integrity of the wood itself and the standardization of production need to be satisfied. There should be no defects, and care should be taken not to reduce the original nature of the product. The drying rate refers to the degree to which the moisture content of the wood itself is reduced in unit time. If the drying speed is relatively fast, the drying equipment and investment that it needs to use will continue to decrease, while the productivity will continue to increase, and the drying cost that it needs to consume will gradually decrease.
When selecting drying equipment in production, it is necessary to confirm according to the tree species and specifications of the wood to be dried, the actual quantity and use, and the actual conditions of the production unit. For a modern wood drying room, it is necessary to keep the temperature and humidity of the drying medium and the air flow speed on the basis of the process, as well as the basic conditions of the external conditions borne by the stacked and dried wood itself, and finally make it possible to achieve a The development goal of uniform drying needs to be safe and reliable in the operation process and flexible in its control, so as to reduce the labor intensity of workers as much as possible. The equipment investment is relatively small, and the land occupation is relatively small, which can take effect quickly, and at the same time, it can keep energy saving, and it is also necessary to reduce the pollution caused to the nearby environment as much as possible.
1.3 The best way to dry wood:
High-frequency vacuum drying is a combined drying method of high-frequency medium heating and vacuum low-temperature drying.
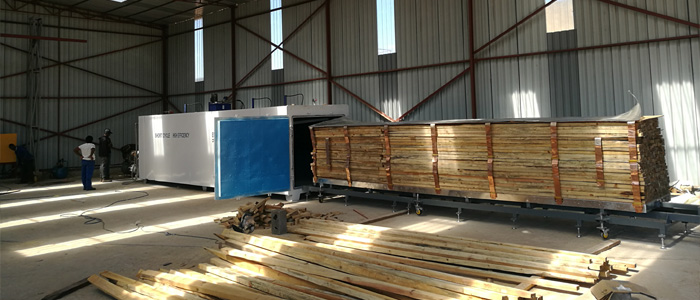
High-frequency wave penetration heating, which penetrates the wood completely and uniformly from the beginning, drying the wood from the core to the surface. Even thick wood heats up well. The water or glue in the electric field is heated evenly at the same time, and only a small amount of high-frequency electric field is absorbed in the place with less moisture, so that the power output by the high-frequency output can be effectively used, and the medium such as wood or fiber is basically not polar because it does not have polarity. Absorb the electric field, so that if the high-frequency power is adjusted to match the object to be heated, the high-frequency power is basically used without waste. Applied to wood drying, high-frequency heating has become a scientific, environmentally friendly and efficient drying method.
High frequency can kill insects (eggs)/fungus in wood, no other special chemical treatment is required.
At the same time, under vacuum conditions, wood moisture can boil at 35-50 degrees and evaporate quickly, which can save time and energy. Low temperature wood drying can preserve wood quality and avoid cracking problems. The vacuum system draws moisture out of the wood due to the pressure difference, thereby doubling the drying speed of the wood. The result of this combination is that our high frequency vacuum wood dryer can dry wood over 50cm thick with uniform moisture content within two weeks. Typically, the drying time for one cycle is 5-6/7-12 days. High drying quality and high yield can reduce waste, save losses, be cost-effective, and bring cost returns in a short time.
The high frequency vacuum wood kiln dryer can be used to dry various wood species, and freshly felled wood can also be directly dried without air drying. It is very different from traditional kilns, which use hot air or steam to dry wood from the surface to the core. 10 times faster than traditional kilns.
Summary:
As an advanced drying method, high-frequency vacuum wood drying technology will have broader prospects in the future wood drying industry, especially in the field of more expensive wood or thicker wood.