The process of drying timber is based on numerous variables. The most common objectives are based on the cost of drying, quick drying time, and reasonable drying quality. To attain a generally acceptable result from these mutually interfering goals, compromises are necessary.

The intricate system of mechanical and physical processes involved in drying timber includes mass and heat flow from outside as well as a coupled mass and heat transport within wood stress-induced shrinkage and deformation and the mechanical memory behavior of wood. Additionally, there are chemical changes that cause discoloration and physical phenomena like cell collapse. Based on this complicated phenomenon, the best practices to achieve a shorter drying time and excellent drying quality are explained in depth, both individually and jointly.
The necessity for drying timber
In order to trigger sap to ascend on trees, the menisci within the leaf stomata draw up water. Since the majority of trees are higher than 10 meters tall The absolute pressure of liquid within the sap column must be negative.

There is no gaseous phase under these conditions. The vascular system that develops in trees can have a variety of effects on the drying process.
- Since the system was built to facilitate longitudinal sap flow from the roots up to the canopy the wood material is highly anisotropic.
- Due to negative pressure that is created by negative pressure, the vascular system has to be able to support the gas infiltration caused by injuries or cavitation. This is why you need pits that are bordered or vessel-to-vessel. These anatomical structures can impede significantly the flow of fluid through the wood.
- In the heartwood, as a result of the deposition of metabolites, aspiration or the closure of pits bordered by borders or tylose formation The permeability can be diminished by one or more orders of magnitudes.
- The wood is totally covered in the sapwood section of the logs (an un-airless sap column needed for negative pressures) The heartwood zone is typically only partially saturated.
To avoid dimensional shifts and other defects, e.g. breaking, warping, and checking because of shrinkage or swelling in the final product The timber must get dried out to moisture content similar to the average for the in-use content. This is the primary reason for drying timber.
The raw material is composed of anisotropy, density, and variation
In the world of wood science, the definition of the product’s raw material is a vast subject which is the reason for this chapter that introduces the reader to the subject. In this chapter, readers will discover a clear explanation of what wood is as well as specific gravity. We also highlight the high anisotropy ratios as well as the huge variation in wood.
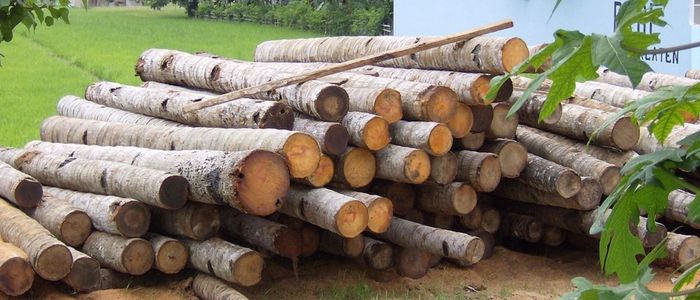
In the end, it is important to remember that because of the secondary growth process, wood is formed to ensure vital roles in living trees, including sap ascent, support for mechanical devices, and endurance.
Thus, as a product, wood is orthotropic and anisotropic. It is a sign of a sizeable amount for the anisotropy ratios that are not dimensionless in wood, for the most significant characteristics involved in drying.
Additionally, even within this same plant, vast variations are evident in the wood’s properties.
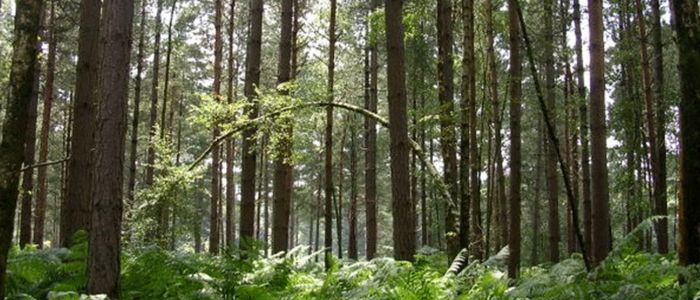
Although a portion of these differences is genetically controlled The most significant variations in drying behavior result from within-tree variations such as sapwood and hardwood and juvenile wood vs. mature wood and reaction wood comparison to. typical wood.
Wood drying is a complicated set of interfering processes
Experts informed the public that dryness is essential and demands a large quantity of water removed from the wood. Understanding modern wood drying is a complex process that requires various causes and consequences to be comprehended.

The reasons are related to factors that affect the process, e.g. drying temperatures, relative humidity, drying medium (air water vapor, air nitrogen …) velocity in convective drying), the thickness of the board,… and physical, mechanical, and chemical properties of wood that change with the amount of wood moisture and temperature.
Drying requires energy that is transferred to the timber. Conduction of heat, heat transfer mass transport, i.e., moisture movement of any kind (liquid flow gas flow, liquid flow diffusion, etc. ) or mass transfers (water evaporate) are processes that are linked interfering. Furthermore, the processes depend on wood characteristics, timing, and the conditions of the environment. Changes in the moisture content of wood and dimensional changes that are related cause drying stress, which is caused by the memory effect of wood. Other effects include chemical changes that cause discoloration and physical phenomena such as cell collapse.
The proportion of time, cost, and quality is the challenge of the wood drying process. The three main goals need to be synchronized to maximize the drying process.
The mechanics and mechanics of wood drying
In terms of the science (physics and chemistry), mechanical and chemical engineering) …) wood drying is a highly complex and intricate phenomenon.

A comprehensive explanation of these processes, including transfer mechanisms and mechanics and the mathematical and physical formulations, is the principal goal of this text. The most significant phenomena in drying wood and the interconnected complexity of these phenomena.
- Mass transfer and heat conduction in porous media
- growth of the moisture content and the temperature field
- Drying field shrinkage and induced stresses
- The mechanical characteristics of wood, leading to casehardening and stress reversal
- Specific effects, such as the casehardening process, discoloration, and collapse
Between the various the couplings between these mechanisms certain couplings are crucial to comprehend drying issues: Deformation and stress formation originate from the temperature and moisture fields (i.e. variations across thickness and the length of the piece that are being dried) through shrinkage Wood’s mechanical behavior is significantly affected by the temperature and moisture levels and also by the time-dependent change in the moisture contents (mechano-sorptive effects), large displacement fields alter the geometry of the original significantly, and also alter the transfer conditions

Wood drying phenomenon
- Stresses that exceed that of the rupture modulus can lead to the examination of changes in the parameters of transfer
- Chemical degradation is closely dependent on the level of moisture content as well as temperature levels and the length of time drying conditions.
- With high values for moisture flux in the presence of high moisture flux values, the extractive deposition could occur near the surface of the exchange, and the exchange will become impervious, leading to extremely long drying times and stress levels that are high.
- The cause of the collapse is capillary forces. It is also caused by temperatures that are high and zones of tension in the peripheral zone.
- Discoloration requires oxygen as well, specifically moisture and temperature levels.
It is difficult to optimize the drying of one board, so how do you manage a whole collection of boards? In reality, a stack is constructed from pieces of wood made from various parts of a single log.
Mechanics of wood drying

- A flat sawn wood board typically is dried along its radial axis with shrinkage occurring in its tangential directions drying fast at the highest stress level and has greater deformation
- A quarter sawed board typically is dried along its tangential axis with shrinkage occurring in the radial direction. it drys more slowly in an area with less stress and lower deformation
- A piece of sapwood has initial high moisture content and ease of movement of moisture. It can withstand drying rates that are high particularly in the initial stages of the dry process with no mechanical degrading
- Heartwood pieces have an initial low moisture content and the difficulty transferring moisture. The drying process must be monitored carefully before the initial drying process.
- To cut down the duration of the process to speed up drying, only heat and mass transfer must be taken into consideration. A few parameters that are influenced by the load on the kiln are crucial also, but they are controlled. Thickness is a crucial parameter (roughly speaking, the time of the drying process is increased with the increase in the thickness)
- transfer and transport characteristics that the timber exhibits (diffusivity, capillary pressure, permeability thermal conductivity, etc. are determined by the type of wood drying, and can be affected by sawing patterns made during cutting).
- “Drying potential” or “drying potential” of the airflow is measured by the coefficient of heat transfer (increases as air velocity increases) times the variance between the temperatures of the bulb that are dry and wet.
- The air velocity also plays an important part to ensure consistency (of Wood MC distribution) in the stack. However, its impact is less significant as the drying process progresses, and the movement of moisture is controlled mostly through internal transfer and transport and transport.
Strategies to get speedy and effective results
Despite the major contradictions with the supervisory methods discussed above, a swift and efficient drying process can be able to summarize these strategies by identifying acceptable compromises.

Particularly, three main guidelines have been suggested as a basis for achieving the best compromise.
1. The high humidity The only way to guarantee an MC gradient that is low is to decrease the potential for drying (dry bulb – wet bulb) as much as possible. Furthermore, this method results in a high EMC value (only the shrinkage is reflected and the impact of temperature on viscoelastic creep cannot be impeded by a low MC value). But, the elevated relative humidity may encourage the development of mold and/or discoloration e.g. blue stain.

2. The high temperature, specifically a high-temperature setting has a beneficial influence. It increases the internal moisture transfer process and also activates the creep of viscoelastic. However, care must be taken when dealing with species that are sensitive High temperatures can increase the likelihood of discoloration, collapse, as well as thermal degrading wood components.
3. A high air speed: A high air velocity guarantees an even MC distribution across the stack. This, however, increases the energy consumption and could result in the coefficient of heat transfer excessive outside transfer flow, But, be aware that these measures require the temperature to be extremely high and have an elevated relative humidity These conditions could be difficult to maintain for specific types of kilns. This is why the most innovative drying techniques may require innovative kiln technology. It should also be noted that often, the cumulative effects of moisture and temperature.