Some people may look at the more utilitarian aspects of drying kilns from two viewpoints:
- Practical and economical – What are the advantages of kiln drying for the manufacturer and user of lumber?
- The technical and scientific – what are the main phenomena that occur during the kiln drying process, and how is it completed?

Practical and economical
To answer the question”Why is it necessary to dry wood by the use of the kiln-dying method rather than by natural ones?
The following five reasons are offered: It is desirable to dry wood in the kiln:
Reduce the weight and shipping costs
The problem of transport costs which are increasing in severity is the reason for drying the kilns of large quantities of conifers in the southern and western regions to lower the amount of moisture in the stock and the weight of the lumber to levels that are much lower than the normal process of air drying.

The argument for transportation that favors the use of kiln drying is less critical in the case of short shipping distances or when lumber is shipped via water, in which case the rates are based on the bulk of the lumber rather than weight.
To minimize the damage that occurs due to drying by air, such as stain, decay, or warping, insect damage, and the process of checking.
The final goal of kiln drying is a significant one for forest conservation. This was previously mentioned in that context. The losses from air seasoning are often more than believed to be. A study of the western region of American larch showed that 70 percent of the lumber of higher grades was decreased to lower rates through the process of checking or warping. In red gum, there are losses of 35 percent for the stage are to be expected.

The oaks experience very high losses this way and through “honeycombing, “especially in the larger dimensions. The wide sapwood of pines, as well as of the red gum, is rapidly stained by blue stains, as well as other discolorations due to the fungus and mold. Massive losses as a result of the problem are anticipated and can reach 70. By putting the lumber straight into the dry kiln after it has been cut, staining will be avoided entirely.
Decay can also be a significant cause of loss for certain species of yard drying and can be prevented by drying the lumber that is green. Infestation with insects, while much more prevalent in tropical areas, can be found throughout the temperate zones to a certain extent too. It is able to be diminished by proper kiln drying as the heat kills larvae and eggs.
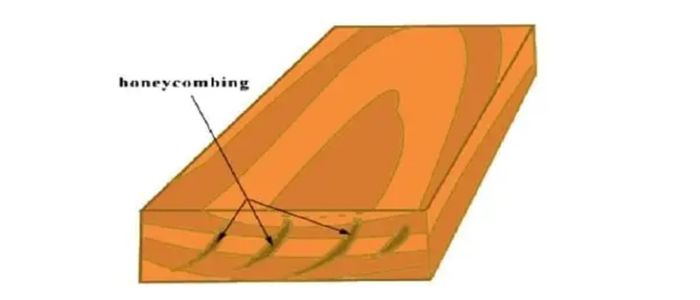
It is clear that the kiln. Drying can be used as an equally sterilizing process to protect against decay, staining, and insect depredation. While it will not make the wood invulnerable to further attacks, there is a lower risk of the lumber being infected once it’s dry than when it is green. In the case of long-distance water shipments, particularly of tropical timbers, there is a lot of damage that occurs as a cause of decay and insect predation and could be avoided by cutting the logs into wood right at the source and then thoroughly drying it prior to shipping.
The wood that remains in the logs will often fall apart before drying. This is particularly true for tropical hardwoods. Losses from air seasoning are varied significantly in different countries and in a variety of instances that no conclusive declaration can be made with regard to their magnitude or the financial losses that are involved. Through the most well-known methods of kiln drying, it is possible to keep losses at a minimum in the best quality of the species, with losses ranging from zero in any way to 5 percent at the outer.

When conifers are in lower grade, the potential savings from drying in kilns may not be as evident due to knots loosening in the event of drying at a moisture content below between 16 and 18 percent. However, many mill operators in the south of the United States partially dry their lower grades of conifers in kilns in order to decrease the weight of shipping.
To avoid the burdensome cost of transport that could be associated with the storage of large quantities of materials in the yard.
The significance of the third purpose of kiln drying is on financial factors that differ with every scenario and can even be an argument in favor of kiln drying. However, the numbers generally favor the drying in the kiln. For hardwoods, the time for seasoning in the kiln as well as in the open air is in an amount that is between the ages of one-to-12 and in conifers in between twenty to one and thirty.
If it is required to transport one-inch lumber each year in the yard prior to it becoming dry enough to be used, this means that you must store one year’s cut of the mill. It includes an interest rate on capital investments, insurance costs, and rental of land and handling charges.
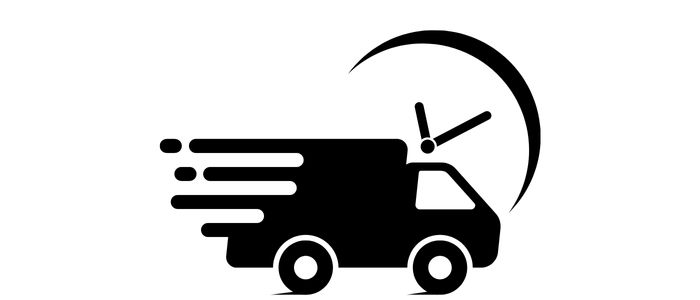
Cost estimates for drying kilns within the United States run from 4.00 per thousand board feet of one-inch conifers quickly dried to $8.50 for ceteris pratibus, hardwoods, and even more than $6.00 for the heavy oak wagons, the price primarily determined by the duration of time needed to run it through the kiln. The time could range between 24 hours and five or four months. Air drying, however, in the case of extremes, could cost just too.
The orders can be completed at short notice, without the need to carry vast amounts of stock in the warehouse.
The importance of the fourth factor is evident, yet it isn’t quantifiable in terms of money. It is clear that if orders are fulfilled by cutting directly from the wood, then it would not be necessary for the operator to carry large stocks of different sizes.
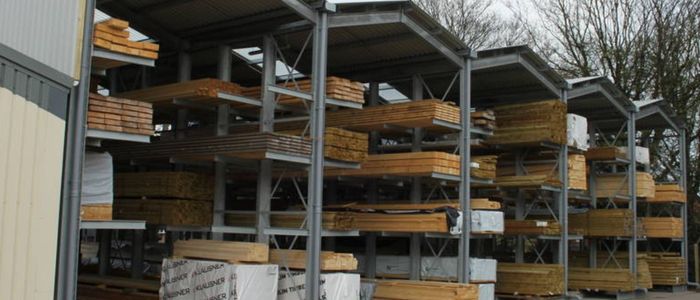
Furthermore, among two mills, one that can fill orders on shorter notice has an advantage over the other that is constrained by the quantity of stock that is already seasoned in stock or must wait for a few months before the newly sawed lumber is able to be dried in the air to the right moisture.
Condition the material to make it suitable for service needs.
The fifth reason to choose the kiln drying process is whether the wood to be dried is green or was prior to being air-dried. In areas with a frigid climate, in which heating in structures is required during a significant portion of the year, the air drying of lumber for furniture and interior finishes is not sufficient for all of the lumber to absolutely be kiln dried (or in the case of the identical process drying in heated buildings) regardless of whether it has undergone prior air conditioning.

In the case of a house that is heated to 70 degrees with the outside temperature of zero degrees Farenheight, in this case, the air will dry out. Tests indicate that relative humidity in these conditions will be only 25-30 percent. The woodwork inside dries within two to three months at a moisture content of around 4 or 5 percent. The shrinkage that results is devastating unless the woodwork is placed into place in an adequately dried kiln.
Paint or varnish can slow down drying but does hinder it if the duration of time during which the house is heated is longer than four or five months. In warm climates or regions where homes are only heated intermittently, Kiln drying isn’t required because the wood will shrink only at all below the air dry conditions.
In those instances in which an air drying condition could suffice, kiln drying could be a great option to ensure that the inside of the board is dried to the minimum standards. It is often the case that lumber may have a moisture content that appears to be adequate for the needs, but, in reality, the interior of the boards is wet. This kind of situation is extremely unpleasant and is always a cause for concern.
The technical and scientific aspects of Seasoning
Wood Physics – To be able to ensure an efficient kiln drying process, it’s not enough to know the principles of evaporation as well as the principles of heat and humidity. Understanding the physical properties of wood and the way it behaves when drying is essential.
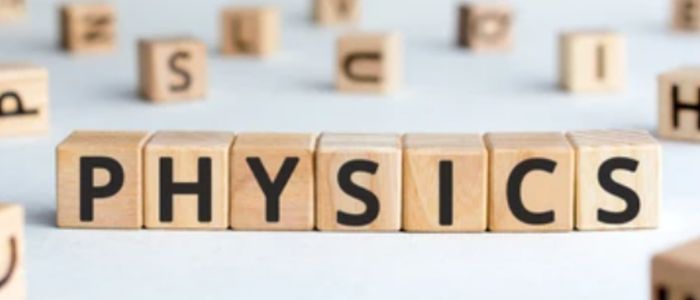
Wood is not an inert material like clay or sand, and the same drying laws are not applicable to it. The force of centrifugal friction equal to 1000 times gravity will not have any impact on the hygroscopic water in the wood and has only a tiny impact on the free water; however, it is not so in highly porous woods, like basswood (linden) and the sapwood (alburnum) of lighter species.
Therefore, centrifugal drying methods like those used to dry clothes are ineffective unless in softer, porous woods. However, there is an American patent granted in 1925 for a drier that was centrifugal, where it was claimed that all free water could be quickly taken off of green wood with centrifugal force and without the use of heat. More research is required to determine which species are affected and to what degree this could be the case.

Wood is a natural material that is built from the most intricate interplay of protoplasm living in the living world and is not considered to be homogeneous or inorganic material. The material from which it is made is probably natural colloidal and comprised primarily of lignocellulose comprising more than 50% of different forms of cellulose. Water is more closely connected to wooden material than other non-combined substances and significantly affects the properties of all its components.
The extraction of wood is a very complex procedure, and the problems are increased with the size of the material. It is not the scope of this article is not sufficient to allow a detailed review of this crucial topic, commonly referred to as Timber Physics. It is essential to mention that, correctly kiln dried lumber is just as sturdy as lumber that has been long-seasoned by air.

This has been proven by more than 300,000 tests on mechanical properties conducted in the United States Forest Products Laboratory. Wood can be damaged, however, due to high temperature or through incorrect manipulation. A thorough kiln drying process has been shown to reduce the hygroscopicity and, consequently, its tendency towards ” work, “‘that is, it makes it a little more stable than drying by air. The technical aspect of the topic that deals mainly with the development of dry kilns and their operation and the instruments to measure and control conditions are not covered in this article because the subject is too vast.
To find out more about kiln drying, feel free to contact us.We would like to discuss this together.